Akkerman operator‐controlled Haul Units transport spoil from the conveyor to the dirt bucket, along the track in the tunnel to the launch shaft for soil disposal.
Our Haul units are electrically driven, propel forward and reverse, and equipped with regenerative disc brakes.
Haul Units are available in two sizes in standard and extended lengths to complement our family of TBM models and dirt buckets. Two track gauge widths are available for efficient spoil transportation on all pipe jacking projects.
The largest capacity Haul Unit can be configured to trolley tandem dirt buckets on the large‐diameter projects.
Features:
- Haul Unit/Muck Cart systems for 36‐in.+ minimum ID tunnel sizes
- Removable battery pack to keep spare to minimize downtime
- Regenerative motor braking
- Inching control for precise propulsion
- Front and rear lights with flashing blue beacon
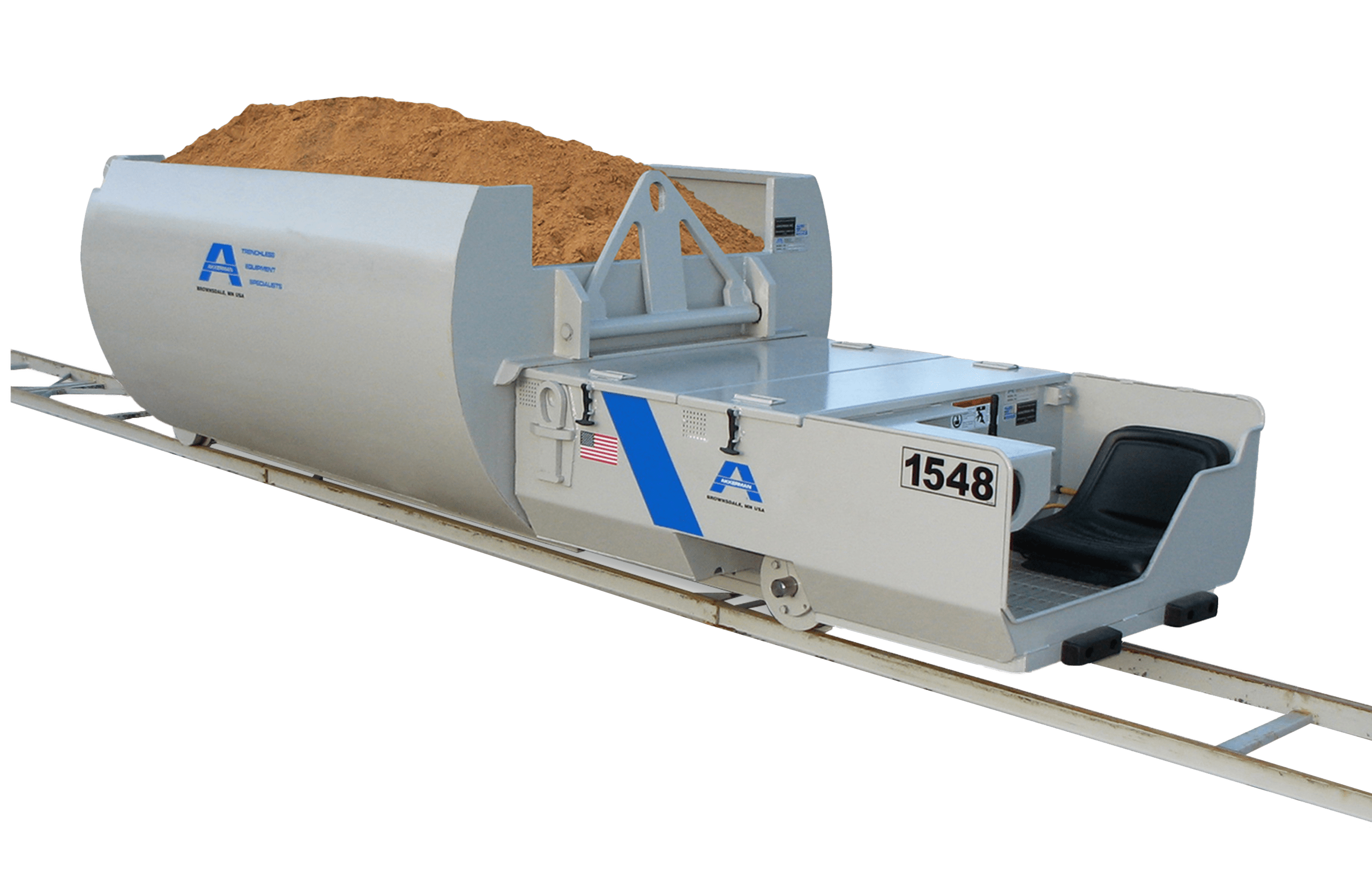
1548 Haul Unit
524 Haul Unit
Specifications
Electric Haul Units
Model | Tunnel ID / Track Gage | Voltage / Speed | Dry Weight / Capacity |
---|---|---|---|
524 HU | 36 in + 11.13 in | 24Vdc 0-4 mph | 950 lbs 8,200 lbs |
1548 HU | 60 in + 20 in | 48Vdc 0-8 mph | 4,800 lbs 20,000 lbs |
Dirt Buckets
Model | Tunnel ID | Capacity | Weight |
---|---|---|---|
DB-360 | 36 in + | 0.8 yd3 | 430 lbs |
DB-420 | 42 in + | 1.1 yd3 | 500 lbs |
DB-480 | 48 in + | 1.5 yd3 | 550 lbs |
DB-540 | 54 in + | 1.8 yd3 | 700 lbs |
DB-540X | 54 in + | 2.7 yd3 | 1160 lbs |
DB-600 | 60 in + | 2.2 yd3 | 830 lbs |
DB-600X | 60 in + | 3.3 yd3 | 1540 lbs |
DB-720X | 72 in + | 4.5 yd3 | 2000 lbs |
DB-780X | 78 in + | 5.0 yd3 | 2350 lbs |
- Custom dirt bucket sizes available upon request
Testimonials
Mextune / Group S de RL de CV
In recent years we have acquired different spare parts for our Akkerman brand TBMs, which have allowed us to have the equipment ready. We have used our tunnel boring machines in 2 emergency projects recently:
- Completion of the construction of the El Valle Collector, with reinforced concrete pipe of 2.13 meters inside diameter for the municipality of Tlajomullo de Zuniga Jalisco.
- Construction of the Jamapa Collector in the municipality of Ecatepec de Morelos (New construction). With 1.22m RCP pipe.
